Why Performance Driven Management?
In A Word: Results
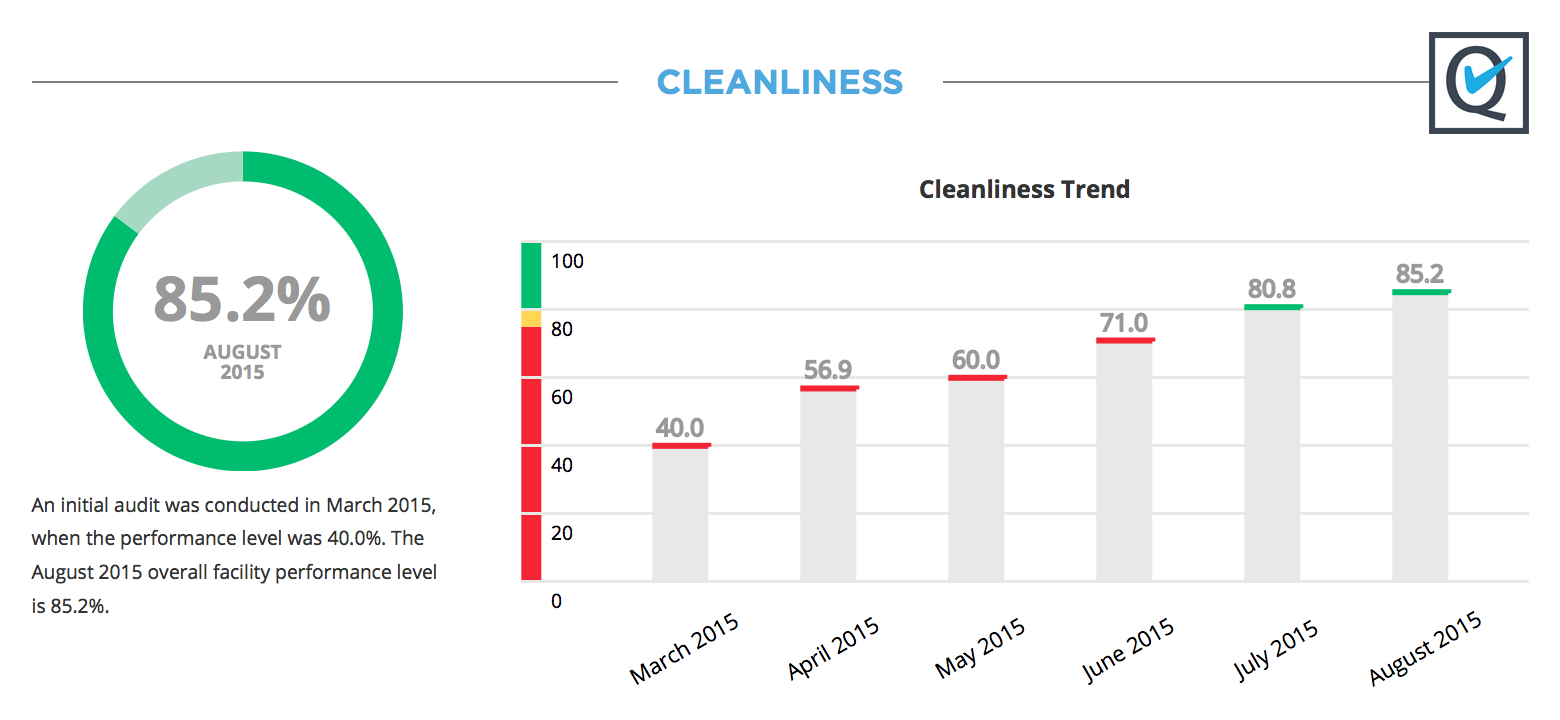
If there is one reason to use the Performance Driven Management (PDM) system, it would be Results. PDM has been used for over 40 years by a private consulting firm to monitor the cleaning performance of facilities to improve results. There are over 900,000 data points used to refine and focus the performance measurement effort on delivering the information that will drive your results – your success!
What’s different with the PDM System?
Typical inspection programs measure facility appearance using a subjective rating system such as poor-to-excellent or a 1–5 scale, etc. drawing on past performance. Add two or more inspectors, and you’ll get multiple ratings of performance. It is not enough to simply measure someone’s subjective opinion about performance. There are two scientific rules about inspection validity that apply here:
- Repeatability: Regardless of how many different people conduct the research (or inspection), validity is achieved when consistent, repeatable results are achieved.
- Variability: Regardless of how many different people conduct the research (or inspection), validity is achieved when the variability of the results are minimized.
There are two reasons to measure facility appearance: to fix problems by identifying underperformance; and to prevent problems by understanding their root cause. Of the two benefits from performance measurement, prevention is the most powerful by far.
PDM was built on the foundation of problem prevention and makes continuous improvement one of the four key metrics for tracking and identifying the root cause of performance failure:
- Cleanliness Quality Appearance
- Occupant Satisfaction
- Environmental Safety and Health
- Process Innovation and Improvement
The Foundation of the PDM System
The PDM system was created by Vince Elliott of Elliott Affiliates, LTD. as a comprehensive and proven problem-prevention system that has delivered results to clients for over forty years. The PDM system for measurement and improvement is grounded in quality principles championed by W. Edwards Deming, Joseph Juran, Phil Crosby, and other quality visionaries. Elliott adapted these quality principles to janitorial service inspection and management. The approach is outlined below:
How the PDM System Works
Performance Lifecycle - Define, Measure, Manage and Improve
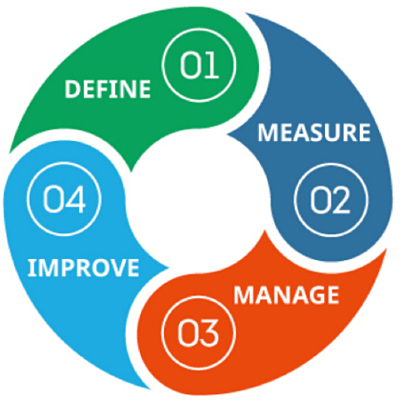
DEFINE Your Success.
While straight-forward, the start of effective performance management is to define the success standards you expect and are to measure. In other words, what are you going to inspect and what standards do you want to achieve. An example of defining cleanliness standards would be setting expected appearance targets for cleanliness quality for each room type in your building. You might expect different standards of cleanliness performance by type of space: For example, the loading dock might have lower expectations than the restroom.
MEASURE Success; Measure Failure.
Once you have defined your success and defined your performance expectations, you’ll want to measure your success against these standards. Performance measurement will highlight those rooms that are meeting your success targets and also will highlight the rooms that are not meeting the targets. This information will help you allocate labor and other resources to improve performance. For example, if the loading dock is exceeding your quality targets, you may want to reduce the effort and resources in that space to focus on rooms not meeting the expected standard.
MANAGE Through Information.
The right performance measurement information can create a roadmap for managing your service delivery program. This is done through understanding the FABRIC structure of report information and using these findings as actionable steps for improvement. PDM’s multi-tiered reports provide the analysis you need for effective management (see more in reports).
IMPROVE Performance.
Typically, inspection programs are about finding and fixing problems – which are likely to reoccur. Sustainable performance success is focused on finding and preventing problems.
A problem prevention model explores the root cause of the problem and then takes action to correct that root cause. Root cause issues are described by W. Edward Deming as Common Cause and Special Cause failures, with clearly defined improvement strategies. For example, if all mirrors exhibit steaks, it may be that the cleaning procedure itself simply does not work (Common cause), or it may be that one cleaner is not performing well (Special cause). In the first case, the solution is a change in the system of cleaning; in the second case, the solution is training of the underperforming worker.
An effective reporting system provides a detailed Management Action Plan to correct both performance improvement opportunities every 30 days. The Management Action Plan is focused on constant process improvement and is powered by the structure of the available information and analysis of that information. An important use of the available information is to ensure that the details produced assures that you can minimize resources in your problem prevention strategy.
How to Deliver More Results Using Fewer Resources
The FABRIC of Information
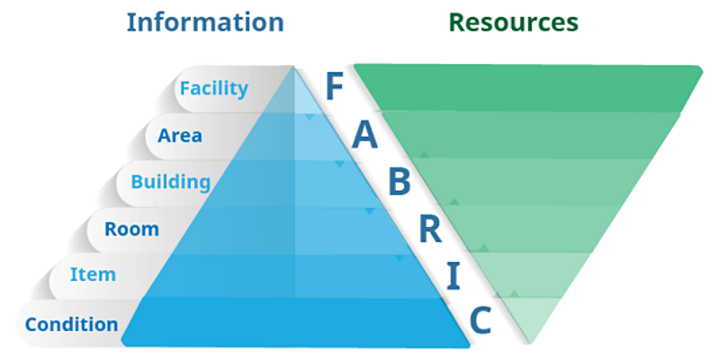
The more specific information you have about your facility’s cleanliness performance, the fewer the resources you have to deploy to achieve your defined standard quality level. How much information detail will reduce resource expenses?
Facility.
If the only performance information you have is limited to a single overall cleanliness or satisfaction rating of your Facility, you are likely to expend substantial resources trying to correct everything that might be wrong in the whole facility.
Area.
If your buildings are grouped into areas, and you have a bit more information at that level, you will continue to expend a great deal of labor and other resources (although less than the entire facility) in the underperforming Area.
Building.
If you have cleanliness performance information at the building level, you are a step closer to reducing the resources needed, even though you are now committed to service in the underperforming building(s).
Room.
Given clear Room-level information, you will expend less time and fewer material resources. Nonetheless, you still have to “clean everything” in that room category to effect an improvement in cleanliness performance. Yet, this is how most cleaning improvement programs are designed – to fix problems in each room. There is a more efficient and effective strategy available from the PDM system.
Item & Condition.
PDM goes beyond fixing problems by tracking the conditions of the items in the rooms – enabling you to focus on the exact item and condition (and associated task) that caused the performance failure, condition, or defect. This attribute-based approach goes beyond the “find and fix” paradigm and enables you to focus on a “find and prevent” model, where the resources are conserved and real savings are found. So, what is the “attribute” idea?
Attributes, not Opinions
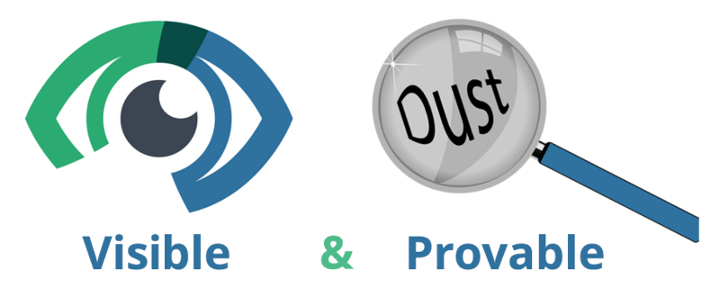
PDM is designed so that performance measurement guides the inspector to focus on cleaning defects, which we call “attributes.” To qualify as an attribute, a condition must be visible and provable. That means something you can see can be seen by others, regardless of who or how many evaluate performance. This objective of attribute-based measurement of cleanliness performance ensures that the objective reliability of the information provided will support a prevention focused management strategy.
Even soil that you cannot see can be made visible with the right equipment. For example, organic soil loads can be detected with the use of an ATP meter that measures the organic matter on touch point surfaces. PDM can track these readings and provide analytics along with other improvement information.
Surfaces and Items, not Rooms
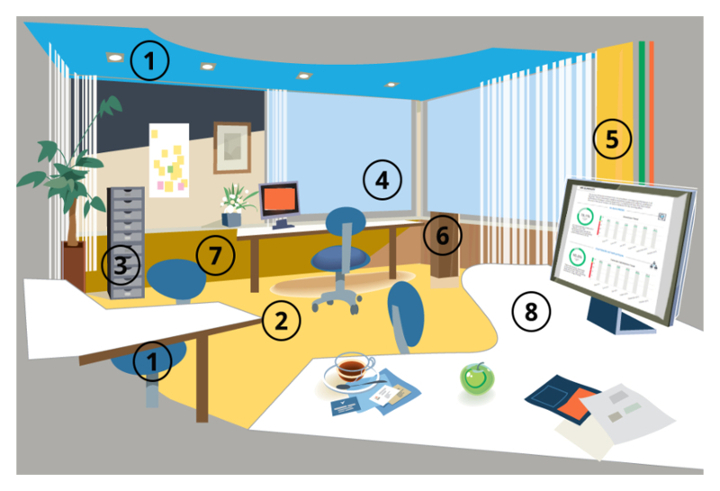
The core of PDM’s functionality begins with a focus on items and conditions as the target of inspections (performance measurement). While items are in a room, going beyond the room and attaching the attribute to each item to the cleaning task is the key to focusing your efforts and understanding how to improve the cleanliness of your building quickly and easily.
Fundamentally, when the provided information allows you identify the item and the attribute (condition) that cause a cleaning failure or defect, you can change and improve the one task used to clean that item to prevent future failure. This is because not all attributes (dust, streaks, buildup, etc.) are cleaned in the same way; even the same attribute may be corrected using different procedures and equipment.
The item cleanliness analysis that PDM report provides the specificity to determine not only how you fix the cleaning system failure, but also how to prevent it. In short, the PDM system will design a customized worker-training and systems innovations and improvement program for you.
The result – your result – is a cleaner facility, more satisfied occupants, a healthier, safer environment and a path to lower cost.